Most cottages in the countryside are heated by burning wood in a simple stone hearth. The desired heat is controlled by the feeding of wood. Today computers manage heating systems in large buildings and the boiler has become almost secondary. A similar trend is evolving with batteries. Increasingly, batteries are being controlled by a device called a Battery Management System (BMS).
The BMS assures safety, long life and provides state-of-charge (SoC). Current systems do this by measuring cell voltage, current and temperature, some also include coulomb counting. Coulomb counting measures the in-and out-flowing battery current, a theory that goes back 250 years. The accuracy of the SoC is good enough for consumer products and it decreases with use and time. By then the user has gotten used to the quirks of the device and no one gets hurt. Military, medical and other critical instruments demand higher accuracies and this article focuses on the intelligence responsible to measure battery SoC.
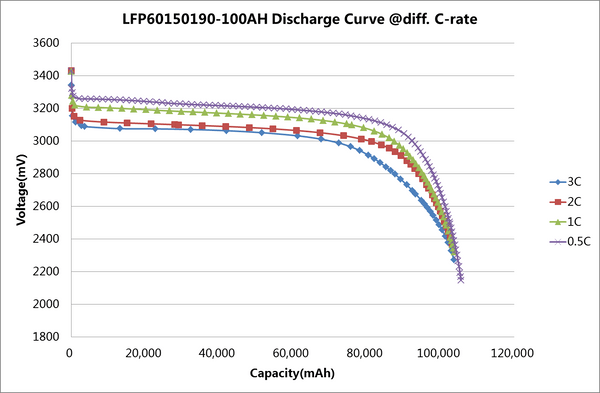
The challenge of the so-called “smart battery” is keeping the electrochemical battery and the digital battery together. The electrochemical battery is known as the actual energy storage vessel and the digital battery is the circuitry that predicts the remaining energy. Figure 1 illustrates the drifting apart of the digital battery from the electrochemical battery and how periodic calibration corrects the error. The values are assumed and accentuated.
|
Figure 1: Tracking of Electrochemical and digital battery as a function of time With use and time the electro-chemical and digital battery drift apart; calibration corrects the error. |
All batteries have losses and the released energy is always less than what has been fed into the pack. Inefficiencies in charge acceptance, especially towards the end of charge, resistive losses that turn into heat, and storage losses in the form of self-discharge reduce deliverable energy. A common flaw with BMS design is assuming that the battery will always stays young and energetic. Aging takes on many dimensions and some BMS compensate by observing user pattern and environmental conditions to derive a “learn” algorithm that is meant to correct the tracking error. Such modelling helps but there are limitations because battery aging cannot always be tracked accurately.
Calibration, also known as capacity re-learning, is a better method to correct the tracking error of a smart battery. Manual calibration occurs by running the battery down on purpose. This can be done in the equipment or externally with a battery analyzer. With most fuel gauge chips, a full discharge resets the discharge flag and the subsequent recharge sets the charge flag. Establishing these two flags allows SoC calculation by tracking the distance between the flags. The calibration of a device in constant use should be done once every three months or after 40 partial cycles. If the device applies a periodic deep discharge on its own accord, no additional calibration is required. Such calibration is practical for a portable device but not an electrical powertrain or UPS.
A device that often runs into calibration problems is a defibrillator. A defibrillator provides shock treatment to a patient suffering from a cardiac arrest. This medical instrument seldom reaches the full discharge needed for self-calibration, and applying a full charge alone is not sufficient. Nor does the SMBus help. SMBus provides communications and the results are only as good as the available data.
Nowhere is the accuracy of the battery fuel gauge more critical than in the electric powertrain. Surveys show that range anxiety is one of the largest concerns among EV buyers. A less known but equally worrisome impediment is inaccuracies in the battery fuel gauge. EV drivers have run out of battery power while the fuel gauge still indicated a comfortable 25 percent reserve. Getting stranded on account of false readings adds fear and paranoia. Anecdotal comments made by engineers at a SAE Consortium reveal that the SoC error of new EV battery modules can be as high as 15 percent.
The fuel gauge of the combustion engine does not have this problem. The storage tank stays the same for the life of the vehicle and the fuel dispensing remains accurate. The battery in the electric vehicle, on the other hand, shrinks and technology to measure dispensed energy needs improvement. People compare the battery with a fuel tank, but estimating storage capability and measuring battery energy from an electrochemical device is far more complex than with a liquid fuel storage system.
The BMS of an electric powertrain should also indicate the total energy a battery can hold at any given time. Accurate capacity measurements are not yet feasible and the losses are mostly hidden to the user. The battery capacity may have dropped to 80 percent, but the BMS will still show 100 percent SoC after a full charge. A lower capacity reduces the runtime and shortens driving range. A weak battery also charges more quickly because there is less to fill.
A BMS should display SoC and SoH. But even if SoH were available, many manufacturers would be hesitant to show a capacity that is less that 100 percent during the warranty period for fear of customer complaint. The SoH of batteries in consumer products, as well as the electric powertrains could be made available to service personnel through coded access. To compensate for losses and honor the 8 to 10 year warranty, EV manufacturers oversize the battery by 20 percent. This allows for aging and offers extra driving range, just in case.
Improving the BMS
Battery voltage, current and temperature alone are not sufficient to provide accurate SoC estimations, much less state-of-health (SoH). Early Li-ion correlated the rising internal resistance with SoH. This no longer works because most modern Li-ion batteries maintain low resistance as the battery ages.
When designing a BMS, one also must consider how the battery serves the host. In an iPhone and most EVs, for example, the battery is “married” to the host. This enables collecting data for learning. The battery and device co-habitat in a similar way to partners in a good marriage. Batteries for two-way radio, on the other hand, are picked from a common charger and returned to a pool for recharging after use. Learning is difficult and a different method must be used to track battery health.
Cadex Electronics is making critical progress in measuring battery SoC with magnetism. Quantum magnetism (Q-Mag™) could provide the most accurate battery SoC readings ever achieved. Q-Mag™ makes use of the magnetic property relating to SoC, which changes as much as three-fold between empty and full charge on some battery systems. A coil generates an AC field and a sensor reads the magnetic susceptibility, which is linear to SoC.
There are several choices of sensors and because of availability and low price Cadex conducts the research with the GMR (Giant Magnetoresistance) sensor. It consists of ferromagnetic alloys that are sandwiched on an ultrathin nonmagnetic conducting layer. Applying a magnetic field lowers the resistance; removing the force increases it. The principle is known as electron scattering, which is also used on hard drive read/write heads. Figure 2 illustrates the function of a GMR sensor.
|
Figure 2: GMR sensor The magnetic property of a battery changes with SoC. A sensor reads the change when exposed to a magnetic field.
|
Q-Mag™ has successfully been tested with Li-ion-cobalt, NMC, lithium iron phosphate, as well as several types of lead acid batteries. The system is immune to most outside interference and does not rely on voltage for SoC estimations. This allows reading SoC while the battery is on charge or a load. Q-Mag™ works with prismatic and cylindrical cells in aluminum and stainless steel casings, but not in ferrous material. The accuracy on lithium-based chemistries is +/-5%, lead acid is +/-7%. This high accuracy should be retained as the battery ages. Calibration occurs by applying a full charge.
With voltage and current references, Q-Mag™ is able to calculate SoC and SoH. The BMS can also detect micro-shorts by observing the self-discharge of a faulty cell, a feature that enhances battery safety. Furthermore, Q-Mag™ can be used for load leveling. This eliminates the rubber-band effect that complicates SoC estimations through voltage. Figure 3 shows Q-Mag as key contributor to BMS.
|
Figure 3: Q-Mag serves as Q-Mag simplifies the BMS and allows state-of-health |
Q-Mag can be made small and sandwiched between cells. A multi-cell battery may have one sensor for an overall assessment or several to enable diagnostics to cell level. An ASIC containing Q-Mag™ could also include temperature sensing and digital processing. At high volume, low price would make this technology available for big and small batteries, including consumer products. Displaying precise energy reserve, as is possible with a liquid fuel system, may be closer than we think.